常規(guī)能源資源短缺和利用中嚴重的環(huán)境污染已成為制約我國經(jīng)濟增長和社會可持續(xù)發(fā)展的主要因素。生物質(zhì)能源由于具有資源豐富、可再生且分布地域廣、可實現(xiàn)C02零排放、大氣污染物排放少等優(yōu)點,被認為是21世紀最有前途的綠色可再生能源之一。我國每年可產(chǎn)生7.05億t秸稈,占我國生物質(zhì)資源的50%以上,但是,除了一部分用作還田肥料和動物飼料外,大部分被廢棄或就地焚燒,不但浪費了寶貴的能源,也給空氣帶來污染,甚至影響公路交通和民航運行。為了有效利用生物質(zhì)能,減少環(huán)境污染,增加農(nóng)民收入,我國從丹麥引進了先進的生物質(zhì)直燃鍋爐技術(shù),近年來已經(jīng)有10余臺投入商業(yè)運行。為消化吸收引進的先進技術(shù),了解生物質(zhì)鍋爐性能特點,山東電力研究院與國能生物發(fā)電公司對1臺130t/h生物質(zhì)直燃發(fā)電鍋爐進行了性能試驗研究,富通新能源銷售生物質(zhì)鍋爐,生物質(zhì)鍋爐主要燃燒木屑顆粒機壓制的木屑生物質(zhì)顆粒燃料。
1、鍋爐概況
本鍋爐為濟南鍋爐廠采用丹麥BWE公司先進的生物燃料燃燒技術(shù)制造的130t/h振動式爐排高溫高壓蒸汽鍋爐,為高溫、高壓參數(shù)自然循環(huán)爐,單汽包、單爐膛、平衡通風、室內(nèi)布置、固態(tài)排渣、全鋼構(gòu)架、底部支撐結(jié)構(gòu)型鍋爐,鍋爐簡圖見圖l。鍋爐采用振動爐排燃燒方式,燃料從爐前通過6個螺旋絞籠給料裝置送人燃燒室,爐膛進料口處設有送料熱風,燃料在強風的作用下進入爐膛時被拋至爐排后部,在此處由于高溫煙氣和一次熱風的作用逐步預熱、干燥、著火、燃燒,隨著爐排振動裝置的工作,燃料邊燃燒邊向爐排前部運動,直至燃盡,最后灰渣落人爐前的出渣口;在二、三煙氣通道下方設有落灰口,從過熱器落下的大顆粒沉降灰可從此處排出。過熱蒸汽采用四級加熱,三級噴水減溫方式;尾部豎井布置兩級省煤器,一級高壓煙氣冷卻器和兩級低壓煙氣冷卻器。為了防止低溫腐蝕,將空氣預熱器布置在煙道以外,采用水加熱空氣的方式,分為高壓空氣預熱器和低壓空氣預熱器,高壓和低壓水分別來給水泵和除氧器。高壓空氣預熱器中的水冷卻后進人高壓煙氣冷卻器中吸熱,最后進入省煤器。低壓空氣預熱器中的水冷卻后進人低壓煙氣冷卻器中吸熱,再返回除氧器。送風機入口布置在鍋爐房內(nèi)爐頂附近,可有效降低鍋爐散熱損失。鍋爐設計參數(shù)如下:額定蒸發(fā)量130t/h,主蒸汽溫度54℃,主蒸汽壓力9.2 MPa,給水溫度21℃,排煙溫度124℃,冷空氣入口溫度35℃,空預器出口風溫190℃。
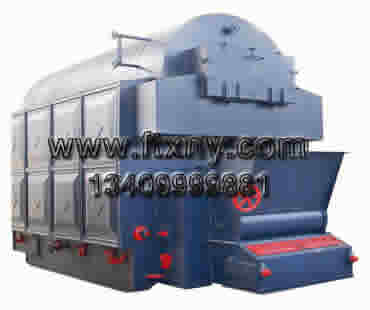
鍋爐設計燃料為棉花秸稈,可摻燒碎木片、樹枝等。設計燃料特性見表1。
2、試驗項目及方法
2.1試驗項目
試驗項目包括鍋爐最大連續(xù)出力試驗和鍋爐熱效率試驗,并在試驗過程中同時測量了NOx排放濃度。
2.2試驗方法
試驗參照CB10184-88《電站鍋爐性能試驗規(guī)程》,采用反平衡法測量鍋爐效率。試驗方法如下:
(1)在低壓煙氣冷卻器出口截面按照等截面網(wǎng)格法,用KM9106煙氣分析儀測量排煙成分(包括02、C0、C02和NOx),用標準熱電偶測量排煙溫度,并送入IMP自動采集系統(tǒng)。
(2)鍋爐飛灰、爐渣和沉降灰采用稱量法測定。飛灰、沉降灰和爐渣分別從布袋除塵器、l、2號撈渣機處進行收集和取樣。
(3)大氣壓力、環(huán)境溫度和環(huán)境濕度在鍋爐房內(nèi)送風機人口測量。
(4)燃料取樣在給料皮帶上進行。
(5)其他運行參數(shù)由DCS采集。
3、數(shù)據(jù)處理方法
GB10184-88《電站鍋爐性能試驗規(guī)程》是針對常規(guī)煤粉鍋爐的,在計算這種類型的生物質(zhì)直燃鍋爐效率時需要考慮以下幾個方面。
(1)鍋爐效率計算基準溫度
常規(guī)煤粉鍋爐的送風機人口一般布置在室外,采用環(huán)境溫度作為計算基準溫度;而本鍋爐料倉和送風機入口均布置在鍋爐房內(nèi),此時由于鍋爐散熱,會導致送風機入口風溫明顯高于鍋爐房外的環(huán)境溫度,如果仍然采用環(huán)境溫度作為計算基準溫度會導致計算鍋爐效率偏低,因此應采用送風機人口風溫作為計算基準溫度。
(2)外來熱源
鍋爐沒有常規(guī)的空氣預熱器,采用給水和除氧器來水加熱空氣,對于給水來說,經(jīng)過了高壓空預器和高壓煙氣冷卻器之后直接進入省煤器,可以不考慮其對鍋爐效率的影響;對于除氧器來水,在低壓空氣預熱器中放熱、低壓煙氣冷卻器中吸熱后重新回到除氧器,實際試驗過程中發(fā)現(xiàn)來水溫度比回水溫度高,因此必須針及除氧器來水對鍋爐的綜合放熱,計算鍋爐效率時可以將低壓空氣預熱器和低壓煙氣冷卻器等效為一個暖風器進行計算。
(3)鍋爐散熱損失
鍋爐設計時采用ASME PTC4.1中的ABMA輻射損失標準曲線,取散熱損失為0. 3%,而根據(jù)CB10184-88中的鍋爐散熱損失曲線得到散熱損失為0. 65%。由于鍋爐為全封閉的,且送風機入口布置在鍋爐房內(nèi),冷卻鍋爐表面的空氣全部用于燃燒,且鍋爐房內(nèi)的空氣溫度高于環(huán)境溫度,因此鍋爐表面的散熱損失應減小,取ASME PTC4.1標準的散熱損失更合理,因此這一項損失仍采用設計值。
(4)鍋爐熱效率的修正
采用送風機入口溫度進行鍋爐效率修正,設計基準溫度為35℃。由于鍋爐低壓煙氣冷卻器設計吸熱量與低壓空氣預熱器設計吸熱量相等,因此效率修正時不考慮二者實際吸熱和放熱量存在的偏差,將低壓煙氣冷卻器和低壓空氣預熱器等效為一般煤粉鍋爐的空氣預熱器,其效率修正可以采用GB10184-88中的方法進行。
4、試驗結(jié)果與分析
4.1鍋爐最大連續(xù)出力
鍋爐最大連續(xù)出力實測值為130.3 t/h,對應電負荷29.9 MW,經(jīng)等焓修正后出力為126.5t/h.未達到設計出力130 t/h。
從鍋爐運行情況來看,其出力受燃料水分的影響較大。這主要體現(xiàn)在兩個方面,第一,鍋爐采用火床燃燒方式,沿爐排長度可以分為干燥引燃段、旺盛燃燒段和燃盡段三個區(qū)域,當燃料含水量增大時,干燥需要更多的熱量和時間,而爐膛溫度降低,使干燥引燃段增長,旺盛燃燒段后移,燃盡段縮短,在水分含量增大到一定值后,會發(fā)生壓火現(xiàn)象,此時增加燃料不能及時干燥并引燃,大量燃料會在燃盡前落人撈渣機,使鍋爐出力反而降低;第二,水分增加使燃料熱值降低,同樣的負荷需要更多的燃料,加劇壓火現(xiàn)象的發(fā)生。鍋爐性能試驗時采用的燃料主要為樹皮并混有少部分棉花秸稈,其化驗結(jié)果如表2所示。
由表2可見,最大連續(xù)出力試驗期間燃料全水分為18.17%,低位發(fā)熱量為13 831 kj/kg,比最差棉稈還低383 kj/kg,試驗燃料水分大、發(fā)熱量低是鍋爐達不到額定出力的主要原因。在日常實際運行時,由于燃料含水分較多,一般在30%—45%范圍內(nèi),其低位發(fā)熱量遠低于設計值,實際運行電負荷一般只能維持在28MW左右。
鍋爐最大連續(xù)出力試驗期間,主蒸汽壓力、溫度等各參數(shù)正常,受熱面不超溫,輔機可以滿足鍋爐出力需要。
4.2鍋爐效率
與電廠協(xié)商后在電負荷28 MW進行了鍋爐效率測定,試驗測量結(jié)果見表3,鍋爐效率計算結(jié)果見表4。
由表4可見,鍋爐實測效率明顯低于設計效率,這主要是由以下幾個方面的原因造成的。
(1)鍋爐排煙溫度高
從表3可見,低壓煙氣冷卻器出口煙溫即排煙溫度比設計值124℃高52℃左右,而人口煙溫僅比設計值207℃高4—5℃,表明鍋爐低壓煙氣冷卻器吸熱量偏低是造成排煙溫度高的根本原因。低壓煙氣冷卻器采用鰭片式緊湊結(jié)構(gòu),容易發(fā)生積灰,加之實際燃用燃料含塵量較大(見表2),加劇了積灰現(xiàn)象,降低了受熱面?zhèn)鳠嵯禂?shù);積灰嚴重時會使局部區(qū)域堵灰,溫度過低形成低溫腐蝕,造成低溫受熱面的腐蝕泄漏,該鍋爐由于泄漏已經(jīng)將低溫煙氣冷卻器堵管5根,減少受熱面積15%。另外,由于送風機出口風溫達到55℃左右,而設計冷風溫度僅為35℃,使除氧器來水在低壓空氣預熱器中的放熱量減小,低壓煙氣冷卻器入口水溫升高,傳熱溫差降低。以上原因造成了低壓煙氣冷卻器吸熱量大幅度下降,排煙溫度上升。目前低壓煙氣冷卻器積灰和腐蝕泄漏現(xiàn)象在多臺同類型的生物質(zhì)直燃發(fā)電鍋爐上均已出現(xiàn),嚴重影響了鍋爐運行可靠性和經(jīng)濟性。
(2)燃料偏離設計值
試驗燃用燃料水分、灰分均高于設計燃料,使燃料低位發(fā)熱量低于設計值,造成各項熱損失均增加,同時燃料灰分增加也使鍋爐排出的灰渣量增加,灰渣物理熱損失增加。
(3)運行氧量偏高
鍋爐設計運行氧量為3%~5%,實測排煙氧量達到7.0%一8.3%,增大了排煙熱損失。
(4)化學未完全燃燒熱損失大
如表3所示,在運行氧量高于設計值的情況下,該鍋爐排煙中未完全燃燒氣體含量較高,可達到0.32%,使化學未完全燃燒熱損失遠遠高于設計值。生物質(zhì)直燃鍋爐采用振動爐排的火床燃燒方式,爐排中間旺盛燃燒區(qū)氧量缺乏,兩頭燃盡段和干燥預熱段氧量過剩,且爐內(nèi)氣體混合較差,不利于揮發(fā)分的燃盡,造成排煙中CO含量很高,特別是在爐排振動時,爐內(nèi)燃燒加劇,CO排放濃度會短時超過l%。從試驗結(jié)果和運行情況來看,要降低化學未完全燃燒熱損失,單純增加運行氧量是不可取的,應通過燃燒調(diào)整,在合理的氧量水平下,優(yōu)化配風,適當增加爐排下中間風室一次風量,減少兩頭風室一次風量;適當增大二次風風速,強化爐膛內(nèi)的氣流混合,保證可燃氣體的燃盡。
4.3 NOx排放
按照GB13223 -2003《火電廠大氣污染排放標準》規(guī)定的方法,測得機組負荷30 MW,排煙氧量6. 84%時NO。排放濃度為120mg/m3,修正到過量空氣系數(shù)為1.4后NOx排放濃度為128ng/m3,遠遠低于燃料含氮量水平相當?shù)拿悍坼仩t,也低于國家制定的燃煤電站鍋爐排放標準450mg/m3,具有良好的環(huán)保特性。
5、結(jié)語
通過對130t/h振動爐排生物質(zhì)直燃鍋爐的性能試驗和分析,得到以下結(jié)論。
(1)鍋爐平均效率為88. 48%,低于設計效率92.0%。鍋爐效率偏低的主要原因是排煙溫
度高、試驗燃料發(fā)熱量低于設計值和化學未完全燃燒熱損失偏高。低壓煙氣冷卻器積灰和低溫腐蝕泄漏后堵管是造排煙溫度高的主要原因。
(2)鍋爐最大連續(xù)出力為126.5 t/h,低于設計值130 t/h。振動爐排生物質(zhì)直燃鍋爐出力受燃料水分影響較大,試驗燃料水分過大、發(fā)熱量偏低造成鍋爐最大出力下降。
(3)鍋爐NOx排放濃度為128 mg/m3(6%02),遠遠低于燃料含氮量水平相當?shù)娜济哄仩t和國家制定的排放標準。
針對生物質(zhì)直燃鍋爐目前存在的問題,建議改進低壓煙氣冷卻器鰭片式緊湊結(jié)構(gòu),采用光管煙氣冷卻器可以減輕積灰,防止低溫腐蝕泄漏,降低排煙溫度,提高鍋爐運行可靠性;通過燃燒調(diào)整優(yōu)化配風,保持合理的運行氧量水平并強化爐內(nèi)煙氣混合以降低化學不完全燃燒熱損失和排煙熱損失,保持較高的效率;進一步研究燃料的儲運方法,加強燃料管理,降低燃料水分,提高鍋爐效率和實際出力。