3000 Ua ADC發(fā)泡劑原有1 000 t/a和2 000 t/a兩條干燥生產(chǎn)線,均為正壓間歇箱式氣流干燥工藝,生產(chǎn)能力小,自動(dòng)化程度低,工人勞動(dòng)強(qiáng)度大,干燥環(huán)境差(主要是粉塵污染嚴(yán)重),安全隱患大,勞動(dòng)生產(chǎn)率低下,產(chǎn)品質(zhì)量不穩(wěn)定。2003年年初,根據(jù)市場需求和公司氯堿發(fā)展的需要,開封東大公司決定建6 000 Ua ADC發(fā)泡劑干燥裝置,同時(shí)要求提高自動(dòng)化水平,提高產(chǎn)品質(zhì)量,為平衡公司氯堿做好準(zhǔn)備。公司技術(shù)人員通過廣泛的討論、學(xué)習(xí)、研究,最終確定了采用負(fù)壓連續(xù)氣流干燥的新工藝。2003年8月開始設(shè)計(jì),經(jīng)過緊張施工、安裝,2004年2月試生產(chǎn)一次投料開車成功。3年多的連續(xù)運(yùn)行證明,干燥裝置能力達(dá)到了6000t/a以上,產(chǎn)品質(zhì)量明顯提高,現(xiàn)場環(huán)境干凈整潔,勞動(dòng)生產(chǎn)率大幅度提高。
1、原有干燥工藝
原有干燥工藝為正壓間歇箱式氣流干燥工藝。其工藝流程:洗滌合格的濕ADC經(jīng)三足離心機(jī)脫水,用行車吊出,間歇投入一級干燥箱,在攪拌情況下與熱空氣充分接觸進(jìn)行干燥,待水分基本合格之后,調(diào)整進(jìn)空氣量。風(fēng)料通過旋風(fēng)分離器,絕大部分ADC進(jìn)入二級干燥箱,夾帶部分ADC的氣流經(jīng)布袋除塵器除塵后排空,留在布袋上的ADC通過人工敲擊也進(jìn)入了二級干燥箱,進(jìn)一步干燥合格后包裝粗品,再搬運(yùn)到振動(dòng)篩分工序篩分,除去雜質(zhì)包裝成品ADC發(fā)泡劑。原干燥工藝流程見圖1。
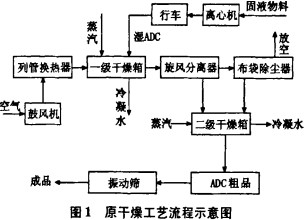
2、原干燥工藝存在的問題
(1)正壓生產(chǎn)易造成干燥的ADC粉末外漏,浪費(fèi)物料并污染環(huán)境;
(2)間歇進(jìn)料干燥系統(tǒng)中的ADC物料較多,存在較大的安全隱患,開封東大公司曾在2000年、2001年出現(xiàn)了兩次較嚴(yán)重的ADC分解事故,造成數(shù)十萬元的經(jīng)濟(jì)損失,均是干燥箱攪拌器與金屬機(jī)械雜質(zhì)摩擦所致;
(3)從離心機(jī)中人工吊料及向一級干燥箱加料,體力勞動(dòng)強(qiáng)度大,易吊壞濾布造成物料浪費(fèi);
(4)粗品搬運(yùn)過篩不僅增加體力勞動(dòng),浪費(fèi)包裝及物料,而且干燥ADC容易吸潮而難以過篩,尤其是在陰雨天,更易造成ADC發(fā)泡劑成品水分超標(biāo),造成結(jié)塊而影響質(zhì)量;
(5)旋風(fēng)分離器內(nèi)的物料和布袋除塵器內(nèi)的物料未分開,造成ADC粒徑分布寬,使產(chǎn)品在使用時(shí)存在發(fā)泡周期長、不易控制以及有效發(fā)泡體積小等缺點(diǎn);
(6)自動(dòng)化程度低,勞動(dòng)生產(chǎn)率低。
3、干燥工藝的改造
針對上述存在的問題,開封東大公司設(shè)計(jì)人員最終設(shè)計(jì)了負(fù)壓連續(xù)氣流干燥新工藝。其工藝流程見圖2。
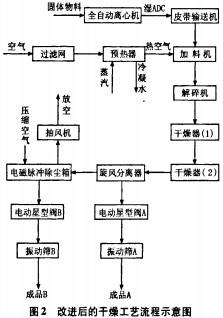
工藝過程:空氣由引風(fēng)機(jī)經(jīng)空氣過濾網(wǎng)吸入,經(jīng)板翅式換熱器與蒸汽間接換熱升溫后進(jìn)入加料機(jī)風(fēng)管,與經(jīng)全自動(dòng)離心機(jī)脫水由皮帶機(jī)輸送來的濕ADC混合,經(jīng)解碎機(jī)破碎,在熱空氣的吹送下進(jìn)入干燥器,在兩級干燥器中不斷除去水分,風(fēng)料進(jìn)入旋風(fēng)分離器,95%的干ADC通過星形閥振動(dòng)篩包裝并稱質(zhì)量,得到成品A。細(xì)小的ADC被熱風(fēng)帶入電磁脈沖除塵箱.干ADC吸附在除塵箱布袋上。水分由熱空氣夾帶,經(jīng)引風(fēng)機(jī)抽出放空。用壓縮空氣將吸咐在除塵箱布袋上的ADC吹到除塵箱底部,由螺旋推進(jìn)器經(jīng)星形閥振動(dòng)篩包裝并稱質(zhì)量,得到成品B。
4、改造效果
(1)經(jīng)過3年多的連續(xù)運(yùn)行,干燥能力達(dá)到6000 Ua以上,物料消耗明顯下降。
(2)通過旋風(fēng)分離器的物料與通過布袋除塵箱的物料分別包裝銷售,用戶反映良好。A成品平均粒徑為14~15 pm,B成品平均粒徑為8~9μm,粒徑正態(tài)分布曲線明顯改善,產(chǎn)品質(zhì)量提升了一個(gè)檔次。
(3)物料連續(xù)進(jìn)出系統(tǒng),系統(tǒng)中物料少,安全性大大提高。
(4)采用了先進(jìn)工藝和設(shè)備,自動(dòng)化水平高,操作方便,改善了工作環(huán)境和勞動(dòng)條件,勞動(dòng)生產(chǎn)率提高2倍多。
(5)整個(gè)系統(tǒng)內(nèi)為負(fù)壓,從根本上解決了ADC發(fā)泡劑粉塵外溢的難題,現(xiàn)場環(huán)境干凈整潔,物料損耗降到最少。
5、結(jié)論
新建的6 000 t/a ADC發(fā)泡劑干燥裝置消化吸收了國內(nèi)外同行業(yè)的先進(jìn)技術(shù),提高了自動(dòng)控制水平,勞動(dòng)生產(chǎn)率大幅度提高。增強(qiáng)自主創(chuàng)新的能力和水平,是我們今后工作中應(yīng)堅(jiān)持和倡導(dǎo)的。