北京燕山石油化工有限公司動力事業(yè)部第三熱電站220 t/h水煤漿鍋爐,是由杭州鍋爐廠生產(chǎn)的高壓蒸汽鍋爐。鍋爐的額定蒸發(fā)量為220 t/h,過熱蒸汽出口溫度為540℃、出口壓力為9.8MPa,鍋筒工作壓力為11.28 MPa。該爐為單鍋筒、自然循環(huán)、集中下降管、Ⅱ型布置的固態(tài)排渣水煤漿鍋爐。鍋爐前部為爐膛,四周布滿膜式水冷壁。爐頂、水平煙道及轉(zhuǎn)向室均設(shè)置了頂棚和膜式包墻管,尾部豎井煙道中交錯布置了兩級省煤器和兩級空氣預(yù)熱器。
本臺鍋爐于1999年1月開始安裝.1999年9月整體水壓試驗完畢。根據(jù)水電部頒發(fā)的《電力建設(shè)施工及驗收技術(shù)規(guī)范(鍋爐機組篇)》的規(guī)定,水煤漿鍋爐在投產(chǎn)前需要對水冷壁、省煤器及其給水管線進行化學清洗,對過熱器系統(tǒng)準備在鍋爐蒸汽吹管前進行大流量水沖洗。動力事業(yè)部于1999年11月對本臺鍋爐進行了化學清洗。本文對清洗情況進行介紹,富通新能源銷售生物質(zhì)鍋爐,生物質(zhì)鍋爐主要燃燒木屑顆粒機壓制的生物質(zhì)顆粒燃料。
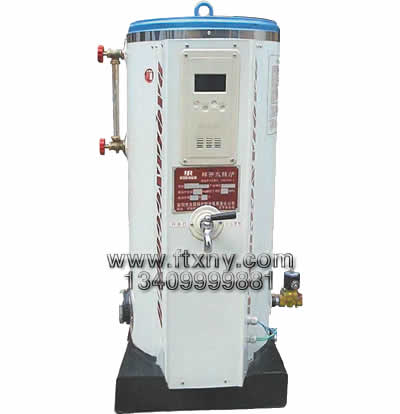
1、鍋爐設(shè)備概況
根據(jù)水煤漿鍋爐工程項目組的要求,本次鍋爐化學清洗只對省煤器、水冷壁、鍋筒、水冷壁上下集箱及給水管線進行化學清洗。因是新鍋爐點火前的化學清洗,本次清洗的主要任務(wù)是清洗受熱面上的油垢、氧化鐵垢、焊渣等沉積物。
1.1省煤器
省煤器布置在尾部豎井中,雙級布置,水與煙氣呈逆流。上、下兩級省煤器均采用順列布置,下級省煤器沿煙道寬度分成左、右對稱兩部分,又沿煙道深度方向分為前后兩部分,形成左右兩側(cè)進水的4組管束。上、下兩級省煤器都由∮32 mm×4 mm的20號鋼管制成,為雙管圈。上級省煤器橫向排數(shù)為73排,下級省煤器橫向排數(shù)為2×23排。給水進入下級省煤器,經(jīng)過爐外12根+76 mmx6 mm的連接管左右交叉引到上級省煤器,再以38根+42 mm×5 mm引出管引至省煤器出口集箱,然后用12根∮76mm×6 mm連接管引至鍋筒。
1.2鍋筒及其內(nèi)部裝置
鍋筒外徑為∮1800 mm,壁厚為100 mm,鍋筒全長為13194 mm,材料為19Mn6。鍋筒內(nèi)布置有旋風分離器,清洗孔板,頂部波形板分離器和頂部均汽孔板等內(nèi)部裝置。鍋爐采用了大口徑集中下降管,為防止入口處產(chǎn)生旋渦斗,在下降管人口處裝有柵格。此外,在鍋筒內(nèi)部還裝有磷酸鹽加藥管,連續(xù)排污管和緊急放水管。
1.3水冷壁
爐膛四周布滿了∮60mm×5mm的光管加扁鋼制成的膜式水冷壁管,形成了一個完全密封的爐膛。水冷壁采用過渡管接頭(∮60mm×5mm/∮45mm×5mm)單排引入上,下集箱。爐膛前、后和兩側(cè)水冷壁均為94根。前墻和兩側(cè)各有∮133 mm×10mm的引出管10根,后墻引出管為∮108 mm×8mm,共16根。從鍋筒最低點引出2根∮377mm×25mm的大口徑集中下降管至運轉(zhuǎn)層以下,再通過分配集箱引出40根+133mm×10 mm的管子分別引入水冷壁下集箱。每根集中下降管供給爐膛一個角部的4個回路,整個水冷壁分為四個大循環(huán)回路。
1.4鍋爐主給水管道
給水由給水母管引入給水操縱臺,通過給水操縱臺實現(xiàn)對鍋爐給水的調(diào)節(jié)和控制。給水操縱臺分成三條管路:Dg175,Dg100,Dg50,分別為100%和70%的負荷及點火管路。由給水操縱臺來的給水端部進入∮219mm×25 mm的分配集箱,再通過12根∮76mm×6mm的連接管從鍋爐兩側(cè)進入下級省煤器集箱。
2、化學清洗的準備工作
2.1鍋爐設(shè)備的技術(shù)數(shù)據(jù)計算
根據(jù)鍋爐設(shè)備的結(jié)構(gòu)特點,鍋爐的各清洗部件的技術(shù)數(shù)據(jù)的計算結(jié)果如表1所示。
2.2被清洗設(shè)備的水容積計算
水容積是化學清洗的一個重要技術(shù)指標。根據(jù)水煤漿鍋爐的有關(guān)技術(shù)資料和化學清洗的施工現(xiàn)場,化學清洗的水容積計算如表2所示。
2.3化學清洗應(yīng)具備的條件
鍋爐整體水壓試驗已完成。鍋爐的水汽系統(tǒng)確與共用系統(tǒng)切斷。鍋爐汽包內(nèi)部的一切設(shè)備都已安裝完畢,并已清理干凈。大直徑的下降管加裝限流孔板,其孔徑為+50 mm,點焊牢固。
要求臨時設(shè)備和系統(tǒng)要經(jīng)受一定壓力、溫度、流量和長時間的考驗,臨時系統(tǒng)的安裝一定要保證安裝質(zhì)量。清洗泵在運行以前必須做好試運轉(zhuǎn)工作,保證化學清洗工作能順利進行。為保證清洗液不進入過熱器管柬,采取割斷汽包頂部的導(dǎo)汽管,焊接堵板進行隔斷。
2.4化學清洗劑的選擇
任何新安裝的設(shè)備及管道,在制造、運輸、儲存及安裝過程中都會不可避免地產(chǎn)生油污、泥沙、焊渣、表面浮層及各種氧化物。在裝置開車前,采用化學清洗的方法,將上述各種污垢、雜質(zhì)清除,使被清洗的表面達到合乎要求的清潔度,為正常生產(chǎn)創(chuàng)造良好的條件。220 t/h水煤漿鍋爐是一臺新安裝的電站蒸汽鍋爐。根據(jù)對鍋爐受熱面的檢查和金屬表面污垢、雜質(zhì)的化驗分析,鍋爐各受熱面上的污垢主要是氧化鐵、焊渣、泥沙和少量的污油。氧化鐵是鋼鐵由于受周圍介質(zhì)的氧化腐蝕,而在其表面生成的以+2或+3價鐵的氧化物或氫氧化物為主的,有時還有少量的其它鐵鹽的沉積物。
220t/h水煤漿鍋爐化學清洗,可采用鹽酸作清洗劑。鹽酸用于化學清洗的濃度一般為5%~10%。鹽酸對鋼鐵有很強的腐蝕性,為了保證被清洗的部件不致腐蝕破壞,往往都采用添加緩蝕劑的緩蝕鹽酸作為清洗液。用鹽酸作為清洗劑,在清洗過程中,必須保證在一定的溫度條件下進行。在清洗過程中,鹽酸清洗液的溫度必須控制在40~60℃。清洗液的溫度低于40℃,清洗速度明顯減小,清洗效果受到很大影響;清洗液的溫度高于60℃,則鹽酸對金屬的腐蝕速度明顯加大,如果清洗系統(tǒng)復(fù)雜,清洗系統(tǒng)的水容積較大,清洗液的溫度就較難控制,這是很危險的。用鹽酸作為清洗劑對金屬表面進行清洗后,必須對其進行鈍化處理。也可選用sw - 101型除垢劑作為清洗劑。SW-101型除垢劑是一種高效、安全、性能良好的復(fù)合型清洗劑。采用該種清洗劑對鍋爐進行化學清洗,清洗工藝簡單。根據(jù)被清洗表面的污垢組成,配制一定濃度的清洗液,采取適當?shù)那逑捶绞,常溫下,在大約6—12 h內(nèi)就可以有效地除去金屬表面的金屬腐蝕物、油污、泥污、焊渣等。該種清洗劑對金屬的腐蝕率較低。與傳統(tǒng)的鹽酸清洗比較,在同樣的清洗條件下,SW - 101清洗劑對金屬的腐蝕率大約為4.00 g/m2.h,遠遠低于國家規(guī)定的10 g/m2.h金屬腐蝕速率。用SW - 101除垢劑作為清洗劑對鍋爐進行化學清洗后,同樣要對被清洗的金屬表面進行鈍化處理。
經(jīng)過分析比較,本次對三電站的220 t/h水煤漿鍋爐進行化學清洗,采用SW -101除垢劑作為清洗劑。
3、清洗系統(tǒng)的組成及清洗過程
3.1清洗系統(tǒng)的組成
本臺爐的清洗范圍包括:給水管線、省煤器、鍋筒、水冷壁、下降管和連接管。清洗方式采用在常溫下循環(huán)清洗的方式進行。根據(jù)本臺鍋爐的結(jié)構(gòu)特點,清洗系統(tǒng)分成三個回路進行。
第一回路:給水總管一省煤器入口聯(lián)箱一下級省煤器管組一上級省煤器管組一省煤器出口聯(lián)箱一鍋筒一四側(cè)水冷壁一水冷壁下聯(lián)箱一清洗罐一清洗泵一給水總管。
第二回路:前墻水冷壁下聯(lián)箱(前墻左側(cè)兩個),左側(cè)墻水冷壁下聯(lián)箱(左側(cè)墻前兩個)一前左側(cè),左前側(cè)水冷壁一鍋筒一前右側(cè),右前側(cè)水冷壁一前墻右側(cè)兩個水冷壁下聯(lián)箱,右側(cè)墻前部兩個水冷壁下聯(lián)箱一清洗罐一清洗泵一前墻水冷壁下聯(lián)箱(前墻左側(cè)兩個),左側(cè)墻水冷壁下聯(lián)箱(左側(cè)墻前兩個)。
第三回路:后墻水冷壁下聯(lián)箱(左側(cè)兩個),左側(cè)墻水冷壁下聯(lián)箱(后側(cè)兩個)一后墻左側(cè)、左墻后側(cè)水冷壁一鍋筒一后墻右側(cè)、右墻后側(cè)水冷壁一后墻右側(cè)、右墻后側(cè)水冷壁下聯(lián)箱(共四個)一清洗罐一清洗泵~后墻水冷壁下聯(lián)箱(左側(cè)兩個),左側(cè)墻水冷壁下聯(lián)箱(后側(cè)兩個)。
3.2化學清洗過程
3.2.1水沖洗
在化學清洗工作進行前用工業(yè)水將清洗系統(tǒng)沖洗干凈,同時對清洗系統(tǒng)進行水壓試驗,以檢查清洗泵的運轉(zhuǎn)情況和清洗系統(tǒng)的嚴密性。
3.2.2化學清洗
根據(jù)SW - 101鍋爐清洗劑的性能特點及被清洗表面的污垢組成,化學清洗采用清洗劑與水以1:10的配比配制清洗液,在常溫下(20℃),采取閉式微帶壓循環(huán)清洗方式進行。在清洗罐內(nèi)配制成規(guī)定濃度的、均勻的清洗液,然后用清洗泵打人清洗系統(tǒng)。清洗液進入清洗系統(tǒng)分三個回路進行循環(huán)。由于本臺鍋爐的水循環(huán)系統(tǒng)比較復(fù)雜,循環(huán)回路較多所以,在鍋爐的化學清洗過程中,要注意觀察每個循環(huán)回路的循環(huán)情況,保證清洗回路的暢通和所需的清洗流量,以保證清洗介質(zhì)的流速。為此,在三個清洗回路的終端,都安裝了一塊流量表,用以監(jiān)督各循環(huán)回路。要把化學清洗介質(zhì)的流速控制在0. 05~0.5 m/s,同時,模擬試驗管段的流速也控制在這個流速,清洗液的pH值控制在1~2,在循環(huán)清洗過程中,每0.5 h,開一次設(shè)在最高處的放空閥,以排出反應(yīng)所產(chǎn)生的氣體。同時,每隔0.5 h,測定清洗液的濃度和pH值,并及時做好記錄,清洗約10 h后,清洗液的濃度基本保持穩(wěn)定,清洗液的pH值恒定在1~2之間,清洗過程結(jié)束。
3.2.3鈍化
鍋爐經(jīng)過化學清洗后,自然氧化膜被溶解破壞,應(yīng)該建立過渡性的保護膜,對被清洗的金屬表面進行鈍化處理,以免產(chǎn)生腐蝕。具體措施是:
配制2%的Na3P04溶液,用NaOH調(diào)節(jié)溶液的pH為9—11,鈍化液溫度控制在90—95℃,對鍋爐進行鈍化,等鈍化液循環(huán)均勻后,靜止侵泡8~12 h,排放鈍化液,鈍化過程結(jié)束。
3. 2.4清洗液的排放
化學清洗工作結(jié)束后,清洗液排至排污溝,并對其進行中和處理(加入適量的NaOH),使廢液的排放應(yīng)符合GB 8978-88的有關(guān)規(guī)定,控制廢液的pH為6~9。
4、化學清洗效果檢查與評價
鍋爐經(jīng)過化學清洗后,要對其進行質(zhì)量評價,根據(jù)對模擬管段,清洗用臨時管段及汽包內(nèi)表面等可見部位的檢查,清洗效果良好。被清洗的金屬表面清潔,無油垢和氧化物等腐蝕產(chǎn)物。鍋爐被清洗的金屬表面沒有出現(xiàn)二次銹垢,沒有出現(xiàn)點蝕現(xiàn)象。金屬表面無明顯的金屬粗晶析出的過洗現(xiàn)象。金屬指示片的腐蝕速率最大為,明顯小于10 g/m2.h的國家標準。金屬表面鈍化效果良好,形成了一層均勻、致密、金黃色的鈍化保護膜。
5、結(jié)語
經(jīng)過周密安排和精心操作,采用了新型復(fù)合清洗劑SW - 101對220 t/h水煤漿鍋爐的化學清洗獲得成功。所選擇的SW - 101清洗劑清洗效果好,對金屬的腐蝕率低,使用安全、方便。清洗后的鍋爐受熱面清潔,無點蝕及二次銹垢,并行成了金黃色的鈍化保護膜,為鍋爐的投入使用打下了良好的基礎(chǔ),富通新能源生產(chǎn)銷售生物質(zhì)鍋爐,同時我們還大量銷售生物質(zhì)鍋爐燃燒專用的生物質(zhì)顆粒燃料。