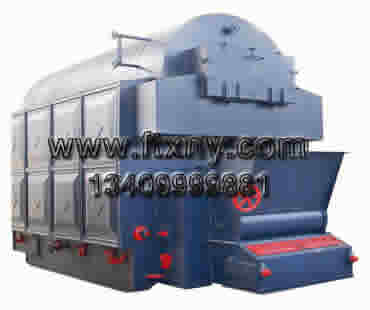
0、前言
某公司現(xiàn)有的2臺(tái)SHF15-2.45A型鍋爐(1#和2#)是先后在2003年和2004年將SHL10-2. 45/A2型鏈條鍋爐改造而成的低倍率循環(huán)流化床鍋爐。鍋爐改造后,燃燒工況非常理想,蒸發(fā)量超過(guò)設(shè)計(jì)能力,熱效率從55. 62%提高到78.00%,爐渣含碳量(質(zhì)量分?jǐn)?shù))從18.55%下降到0.03%~0.20%,節(jié)能效果非常明顯,達(dá)到了改造預(yù)期效果。但目前玉龍公司生產(chǎn)系統(tǒng)較長(zhǎng)時(shí)間處于低負(fù)荷情況下生產(chǎn),按改造后該型循環(huán)流化床鍋爐的最低蒸汽生產(chǎn)負(fù)荷10~ 11 t/h,至少有2 t/h的蒸汽放空。因此,結(jié)合SHF15 -2. 45A型循環(huán)流化床鍋爐特點(diǎn)及使用過(guò)程中的實(shí)踐經(jīng)驗(yàn),對(duì)其低溫回料系統(tǒng)作了進(jìn)一步改造,富通新能源生產(chǎn)銷售生物質(zhì)鍋爐,生物質(zhì)鍋爐主要燃燒木屑顆粒機(jī)壓制的木屑生物質(zhì)顆粒燃料。
1、使用現(xiàn)狀及原因分析
SHF15-2. 45A型循環(huán)流化床鍋爐的回料系統(tǒng)采用高、低溫回料,其改造前結(jié)構(gòu)示意見圖1。
原實(shí)際生產(chǎn)中,低溫細(xì)灰采用間斷性人工放灰,其余的細(xì)灰都返回爐膛繼續(xù)燃燒,因此爐膛內(nèi)各相區(qū)溫差相對(duì)穩(wěn)定。為了降低鍋爐運(yùn)行負(fù)荷,決定將低溫細(xì)灰常放,即降低了爐膛內(nèi)物料的濃度和爐內(nèi)傳熱系數(shù),在給煤速率不變的情況下,爐膛上,下部的濃、稀相區(qū)的溫差加大,循環(huán)倍率進(jìn)一步降低,鍋爐的熱負(fù)荷也隨之降低,從而達(dá)到更低負(fù)荷運(yùn)行的目的。但若采用人工常放細(xì)灰,不僅操作工的勞動(dòng)強(qiáng)度增大,且爐膛內(nèi)沸騰段溫度波動(dòng)大,甚至無(wú)法實(shí)現(xiàn)(細(xì)灰排放量>3t/h)。因此在低溫回料斗下新配1根常放細(xì)灰的落灰管(配有吹風(fēng)管和沖洗管防堵)直接將細(xì)灰排人污水池中,細(xì)灰在污水池中沉淀后用行車將其抓至灰場(chǎng)處理,不僅解決了人工常放細(xì)灰難題,也杜絕了蒸汽放空。
2、效益分析
(1)這次改造所用管材主要為玉龍公司工藝改造時(shí)更換下來(lái)的舊管,每臺(tái)鍋爐的改造費(fèi)用為2000元左右。
(2)改造后,因返回爐膛的細(xì)灰大大減少,熱損失增加,因此煤耗有所提高。按8t/h低負(fù)荷運(yùn)行、噸蒸汽耗煤0.35t、爐膛所放細(xì)灰中含碳質(zhì)量分?jǐn)?shù)為0.02%、常放細(xì)灰中含碳質(zhì)量分?jǐn)?shù)為0.61%、燃煤中含碳質(zhì)量分?jǐn)?shù)為25%、低循環(huán)倍率為5%計(jì)算,則每天煤耗為67.2t,每天少返回細(xì)灰所造成的煤耗為79.65 kg,加上未計(jì)入熱損失并結(jié)合實(shí)際運(yùn)行情況,每天多用燃煤約150 kg。改造后減少蒸汽放空2t/h。
3、實(shí)際運(yùn)行效果
改造后,鍋爐的熱負(fù)荷下降,其煙氣量也隨之減少,引風(fēng)機(jī)的電流進(jìn)一步減小,從而節(jié)約了電能并降低了費(fèi)用。另外,由于循環(huán)細(xì)灰量減少,故減輕了水膜除塵器的壓力,排出的煙氣質(zhì)量更好,減少對(duì)大氣的污染,有利于環(huán)保。
4、結(jié)語(yǔ)
于2011年1月先后對(duì)1#和2#鍋爐的低溫回料系統(tǒng)進(jìn)行了改造。改造后,低負(fù)荷工況下運(yùn)行至今,最低負(fù)荷為近8t/h,生產(chǎn)系統(tǒng)在低負(fù)荷生產(chǎn)情況下不再有蒸汽放空,從而節(jié)約了蒸汽,降低了低負(fù)荷生產(chǎn)時(shí)的生產(chǎn)成本。