Ø2. 8m/2. 4m×40m RSP -4型預分解窯生產線于1979年建成,屬于第一代RSP型試驗窯,設計能力300t/d。自投產以來,通過小改小革,回轉窯烘干機達到了設計能力,但存在能耗高、入窯分解率低及產質量不穩(wěn)定等問題。為此,于2001年3月對回轉窯系統(tǒng)進行了改造,使窯生產能力提高到500t/d以上。
1、存在的問題
1)分解爐爐體容積小,物料在MC室停留時間短,煤粉在爐內不能完全燃燒,常出現(xiàn)分解爐和C4筒溫度倒掛現(xiàn)象,造成預熱器超溫,C3經常堵塞,物料分解率只有40%左右。
2)“V”型三次風管阻力太大,一般為1.0~1.1kPa,積料嚴重,每隔半年需停窯清理1次。
3)預熱器水平管道處易積灰,系統(tǒng)阻力大,分離及熱交換效率低,C.筒出口溫度高,能耗高。
4)預熱器的人孔門、翻板閥及預熱器內筒等損壞嚴重,漏風大,效率低,制約窯產量的提高。
5)C3下料管因設計空間狹小,長度只有1.7m。翻板閥不靈活,經常堵料。
6)窯頭罩偏小,從篦冷機上來的二次風風速高,窯頭飛砂大,密封不易處理,同時二次風影響噴煤管的火焰形狀。
7)篦冷機為2. 2m×12. 6m水平推動式,設計能力為27t/h,因其結構及風室設計不合理,冷卻效果不佳,在窯臺時產量為12. 5t/h情況下,常出現(xiàn)“紅河”現(xiàn)象。
8)篦冷機排風機能力不足,窯頭正壓大,飛砂多,操作環(huán)境惡劣。
9)煤粉輸送系統(tǒng)幾經改造,仍不能保證窯頭和分解爐穩(wěn)定供煤,送煤不暢,煤量不穩(wěn)。
10)早期配套的熱工儀表,靈敏度低,誤差大,對操作工易造成誤導,工藝參數(shù)調節(jié)滯后,影響窯的正常操作。
由于以上問題的存在,致使窯的煤耗、電耗偏高,預熱器堵塞、塌料現(xiàn)象嚴重,窯的產質量不穩(wěn)定。2000年9~12月生產情況見表1。盒式撒料器不僅使用壽命長,而且調節(jié)靈活,拆裝方便,并能充分分散物料,減少股料及塌料現(xiàn)象。
5)對C4旋風筒采用4芯渦殼大斜頂技術進行改造,增加了旋風筒的分離效率,旋風筒阻力降低0. 2kPa,同時取消了內筒,減少了正常的維修資金投入。C4旋風筒結構見圖1。
6)原C3及C4筒的導流板用Cr26N120Si2耐熱鋼板制作,因導流板長期處于高溫腐蝕氣體中,逐步變形腐蝕,一般壽命為1年,F(xiàn)采用耐火澆注料澆注導流板,使用半年后,損蝕非常小,預計可用2~3年,并且造價不到1萬元,僅為耐熱鋼的1半。
7)窯頭罩擴大,降低二次風風速。
8)將篦冷機的風室由1個分成3個,并在入料端采用充氣篦板,增強冷卻效果。改造后,當熟料生產能力提高到30t/h,出篦冷機熟料溫度為70。C,二次風溫(1000 +50)℃,三次風溫750~ 8000C,較技改前有較大提高,保證窯的優(yōu)化操作。
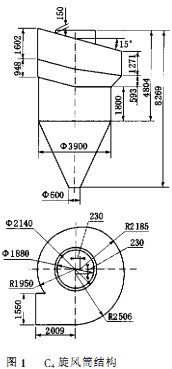
9)篦冷機排風機改為Y4 - 73 -11№14D離心風機,流量87 353m3/h,比改造前增加40 000m3/h。
10)煤粉倉內設高分子材料板,改善煤粉的流動性,消除結壁現(xiàn)象。
11)更新窯頭及分解爐喂煤雙管螺旋喂料機,并將其采取向上傾斜50的布置,同時在雙管螺旋喂料機下增設旋轉給料機,增強鎖風及穩(wěn)煤效果。
12)采用新型數(shù)字儀表,儀表的溫度顯示選用現(xiàn)場式溫度變送器,壓力顯示選用電容式壓力變送器。
13)供料系統(tǒng)新上微機自動控制系統(tǒng),實現(xiàn)自動調節(jié),穩(wěn)定分解爐與C4筒的溫度。
3、技改后的效果
此次工藝技改由山東水泥集團設計院作主體設計,我公司作相應的配套設計。從拆除框架到預熱器的安裝,僅用2個月的時間,于2001年5月1日點火開窯,實現(xiàn)了當月達產,3個月達標。其中5月28~ 31日4d累計生產熟料2 139t,平均日產熟料535t,臺時產量23t/h,熟料熱耗4 368kj/kg,其余各項指標也達到了設計要求。技改前后有關參數(shù)見表2和表3。
三門峽富通新能源銷售木屑烘干機、木屑氣流式烘干機等機械設備。