1、引言
間接換熱式列管回轉(zhuǎn)干燥機(jī)烘干機(jī)(下簡稱列管回轉(zhuǎn)干燥機(jī)烘干機(jī))屬于間接傳熱干燥設(shè)備,它是在傳統(tǒng)的直接換熱回轉(zhuǎn)干燥機(jī)烘干機(jī)的基礎(chǔ)上加裝加熱列管,加熱管內(nèi)可通入蒸汽、熱煙氣、導(dǎo)熱油等作為熱源。干燥所需的熱量由加熱列管傳遞給被干燥的物料。與傳統(tǒng)的直接傳熱回轉(zhuǎn)干燥機(jī)烘干機(jī)相比,列管回轉(zhuǎn)干燥機(jī)烘干機(jī)具有以下優(yōu)點:
(1)產(chǎn)品質(zhì)量易于保證。由于物料與干燥介質(zhì)不直接接觸,避免了干燥介質(zhì)對物料的二次污染。
(2)傳熱面積大,處理能力大。若使用蒸汽作為熱源,還可以方便地回收換熱后蒸汽形成的冷凝水,大大提高熱能的利用率。
(3)高的熱效率。間接加熱干燥機(jī)烘干機(jī)的熱效率主要體現(xiàn)在尾氣流量上,與直接加熱干燥機(jī)烘干機(jī)相比,間接加熱干燥機(jī)烘干機(jī)的尾氣流量小,因而帶走的熱能就少。一般說來,達(dá)到相同的干燥質(zhì)量,間接式干燥機(jī)烘干機(jī)所需熱能是直接式干燥機(jī)烘干機(jī)的1/2~1/3,并且隨著成品目標(biāo)濕度的降低,間接式干燥機(jī)烘干機(jī)1的優(yōu)勢會顯著增加。
(4)低污染。尾氣流量小使從干燥機(jī)烘干機(jī)攜帶出的粉塵也大為減少,可以把污染控制在很小的范圍內(nèi)。同時由于尾氣中濕分的含量可以很高,有利于一些特殊溶劑的回收。
為將干燥過程中脫除的濕份帶出列管回轉(zhuǎn)干燥機(jī)烘干機(jī),保證干燥效果,需向干燥機(jī)烘干機(jī)內(nèi)通入一定量的攜濕氣體。由于與列管和物料顆粒之間均存在熱質(zhì)傳遞,因此,攜濕氣體的引入必然對干燥機(jī)烘干機(jī)內(nèi)的傳熱傳質(zhì)產(chǎn)生影響。同時,攜濕氣流的存在也意味著尾氣的攜帶熱能和粉塵增加?梢,列管回轉(zhuǎn)干燥機(jī)烘干機(jī)攜濕氣體流量的確定,對列管回轉(zhuǎn)干燥機(jī)烘干機(jī)的運行將產(chǎn)生較大的影響。雖然列管回轉(zhuǎn)干燥機(jī)烘干機(jī)已獲得了一些工業(yè)應(yīng)用,然而,目前國內(nèi)外對列管回轉(zhuǎn)干燥機(jī)烘干機(jī)內(nèi)干燥機(jī)烘干機(jī)理的研究很少,攜濕氣體流量仍憑經(jīng)驗確定。同時,在工業(yè)生產(chǎn)中應(yīng)用的列管回轉(zhuǎn)干燥機(jī)烘干機(jī)也有許多是在不合理的攜濕氣體流量下運行的。本文擬對攜濕氣體流量對干燥速率的影響進(jìn)行實驗研究,進(jìn)而確定出列管回轉(zhuǎn)干燥系統(tǒng)合理的攜濕氣體的流量。
2、實驗系統(tǒng)及方法
實際工程應(yīng)用的列管回轉(zhuǎn)干燥系統(tǒng),主要由熱源、干燥機(jī)烘干機(jī)、加料裝置、出料裝置等組成。干燥機(jī)烘干機(jī)內(nèi)脫水所需熱量由列管內(nèi)的熱介質(zhì)(一般為蒸汽)通過管壁向被干燥物料傳遞。因列管隨簡體轉(zhuǎn)動,所以,熱源與列管間須進(jìn)行動連接。這種連接在實驗室實現(xiàn)的難度較大,且不便于瞬時熱流量的測量。為對列管回轉(zhuǎn)干燥機(jī)烘干機(jī)內(nèi)的傳熱傳質(zhì)機(jī)理進(jìn)行實驗研究,我們建立了一套獨特的實驗裝置。
實驗裝置由簡體、不銹鋼列管、電機(jī)、電磁調(diào)速器、電流表、調(diào)壓顯示器、氮氣瓶、氮氣減壓閥、流量計、電加熱器等組成。其流程圖如圖1所示。
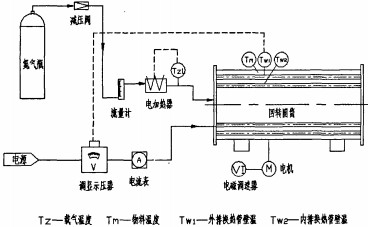
筒體選用不銹鋼材質(zhì),規(guī)格為Ø500mmx675mm。筒體內(nèi)的列管分為不銹鋼管、電加熱管、測試管三種。不銹鋼管用于固定熱電偶,測量物料或筒內(nèi)環(huán)境的溫度。電加熱管做為熱源,為實驗系統(tǒng)提供熱量。每根電加熱管的額定功率為1kw。采用帶反饋的可控硅比例電壓調(diào)節(jié)器調(diào)節(jié)電加熱管的功率,可獲得不同的管壁溫度。并設(shè)有電流表,測量通入電加熱管的電流。電加熱管通過碳刷與電源連接。電壓調(diào)節(jié)器固定于簡體端部,隨簡體一起轉(zhuǎn)動。
在內(nèi)排和外排管的同一徑向位置處,各有一根列管的表面敷設(shè)熱電偶,用以測量列管表面溫度。用于測量物料溫度的熱電偶則埋設(shè)于鄰近這兩根電加熱管的下游不銹鋼管上。每個熱電偶各配有數(shù)顯表,讀取測量溫度值,讀數(shù)精度0.1℃。管壁溫度Tw與調(diào)壓器的可控硅實行反饋調(diào)節(jié),使管壁溫度穩(wěn)定在所需的設(shè)定值上。
傳動系統(tǒng)由調(diào)速電機(jī)、鏈輪、鏈條和托輪組成。簡體通過電機(jī)帶動托輪實現(xiàn)轉(zhuǎn)動,可通過調(diào)節(jié)電磁調(diào)速器來改變筒體轉(zhuǎn)速。
以氮氣作為攜濕氣體,經(jīng)電加熱器加熱后通入筒體內(nèi),攜濕氣體溫度Tz與電加熱器的可控硅實行反饋調(diào)節(jié),改變電加熱器功率,使攜濕氣體溫度Tz穩(wěn)定在所需的設(shè)定值。采用玻璃轉(zhuǎn)子流量計對攜濕氣體流量進(jìn)行調(diào)節(jié)和顯示。
本研究以初始含水量為14%的精對苯二甲酸(PTA)濕物料作為實驗原料。因其粉塵具有容易爆炸的特性,故選用氮氣作為攜濕氣體,同時兼作防暴介質(zhì)。實驗中,維持基礎(chǔ)工況不變,僅改變攜濕氣體流量(0m
3/h,2 m
3/h,3 m
3/h,4 m
3/h,5 m
3/h,6.2 m
3/h),每隔3分鐘對筒內(nèi)物料進(jìn)行取樣,分析含水率,直至達(dá)到小于0.1%的終水份要求。做出每次實驗的干燥脫水曲線,以獲取恒速段干燥速率、臨界含水量、平衡含水量等參數(shù),進(jìn)而分析攜濕氣體流量對干燥速率的影響。盡管本實驗屬于間歇操作,但是,對于連續(xù)操作的列管回轉(zhuǎn)干燥機(jī)烘干機(jī)而言,從加料端至出料端,物料的含水量、水蒸汽與攜濕氣體的比值及物料的溫度等參數(shù)均與上述實驗在干燥時間上具有相同的分布。因此,該實驗對于列管回轉(zhuǎn)干燥機(jī)烘干機(jī)及其系統(tǒng)的設(shè)計和計算具有較大的參考價值。
實驗的基礎(chǔ)工況參數(shù)見表1。
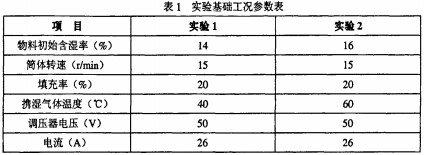
3、實驗結(jié)果及分析
圖2a為在上述“實驗1”條件下獲得的攜濕氣體流量為6.2 m3/h時的lyfA的干燥特性曲線。由圖看出,列管回轉(zhuǎn)干燥機(jī)烘干機(jī)內(nèi)物料的干燥過程可分為三個階段:
(1)物料預(yù)熱階段(a-b段)。在該階段中,由于加熱列管與物料的溫差較大,由列管傳遞給物料的熱量遠(yuǎn)遠(yuǎn)大于物料表面水份蒸發(fā)所需的熱量,故物料溫度迅速升高。此時水份蒸發(fā)速度較慢,因此預(yù)熱段的干燥曲線比較平緩,斜率較低。
(2)等速干燥階段(b-c段)。該階段的干燥曲線基本呈一直線,即該段內(nèi)的干燥速率為一定值。該階段中,物料內(nèi)部水份向其表面遷移的速率能夠滿足物料表面水份的汽化速率要求,所以該階段的干燥速率取決于物料表面水份的汽化速度。(3)降速干燥階段(c-d段)。該階段干燥曲線斜率變小,干燥速率降低。該階段中,物料表面的濕含量低于臨界濕含量,物料內(nèi)部水份向表面遷移的速率低于物料表面水份的汽化速率。該階段的干燥速率完全取決于水份和蒸汽在物料內(nèi)部的擴(kuò)散速度,提高干燥速率的關(guān)鍵不再是改善干燥介質(zhì)的條件,而是如何提高物料內(nèi)部濕份擴(kuò)散速度的問題
如圖2 (b)所示,對于上述干燥特性曲線,對恒速干燥段與降速干燥段用式(1)與式(2)進(jìn)行擬合,即可得出恒速干燥段的干燥速率、臨界含水量、平衡含水量等參數(shù)。
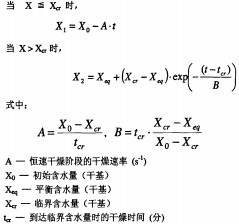
上述“實驗1”和“實驗2”測得干燥特性曲線隨攜濕氣體流量的變化如圖3(a)和圖3(b)。圖中的每一條干燥特性曲線均與圖2 (a)具有相似的變化規(guī)律,而其曲線在恒速干燥段的斜率卻隨著攜濕氣體流量的變化而變化?梢姅y濕氣體對列管回轉(zhuǎn)干燥機(jī)烘干機(jī)的干燥特性具有顯著的影響。
富通新能源生產(chǎn)銷售的烘干機(jī)干燥機(jī)如下所示:
-
適應(yīng)物料:木屑、粉狀顆粒等
設(shè)備類型:烘干機(jī)
-
適應(yīng)物料:顆粒狀物料
設(shè)備類型:烘干機(jī)
對上述干燥特性曲線進(jìn)行擬合后得出的列管回轉(zhuǎn)干燥機(jī)烘干機(jī)的干燥速率與相對攜濕氣體流量(攜濕氣體流量與單位時間脫水量的比值)的關(guān)系如圖4所示。
實驗發(fā)現(xiàn),在本文的實驗條件下,干燥速率開始時隨著攜濕氣體流量的增加而增大。而當(dāng)攜濕氣體流量增加至某一數(shù)值后,干燥速率則隨著攜濕氣體流量的增加反而減小。與干燥速率峰值相對應(yīng)的相對攜濕氣體流量為0.16左右。從能源利用和干燥時間等因素綜合考慮,該攜濕氣體流量既可保證干燥機(jī)烘干機(jī)具有理想的干燥速度,又不會導(dǎo)致過大的尾氣排放。因此,對于列管回轉(zhuǎn)干燥機(jī)烘干機(jī)而言,該流量是最佳的攜濕氣體流量。筆者認(rèn)為,在本文所涉及的實驗范圍內(nèi),在恒速干燥階段,因為相對攜濕氣體流量小于0.3,攜濕氣體處于超飽和狀態(tài)。此時,列管回轉(zhuǎn)干燥機(jī)烘干機(jī)內(nèi)的脫水過程可以看作過熱蒸汽干燥。
過熱蒸汽干燥與熱風(fēng)干燥在傳質(zhì)機(jī)理上具有較大的差異。氣體對流干燥的傳質(zhì)動力是物料表面與氣體的濕度差,而過熱蒸汽的傳質(zhì)動力則源自物料表面與其環(huán)境的壓力梯度。在列管回轉(zhuǎn)干燥機(jī)烘干機(jī)中,與物料接觸的列管為物料的水分汽化提供熱能,與水汽接觸的列管則加熱蒸汽使其成為過熱蒸汽。過熱蒸汽干燥速率取決于蒸汽的過熱度、蒸汽的流速、蒸汽壓力等因素,蒸汽的過熱度越高、蒸汽流速越大、蒸汽分壓力越小,干燥速率越大。而攜濕氣體的引入一方面提高了蒸汽的流速,減小了水蒸汽的分壓力。另一方面,攜濕氣體也與干燥機(jī)烘干機(jī)內(nèi)列管、物料和蒸汽存在熱交換,從而影響蒸汽的過熱度。
實驗還發(fā)現(xiàn),如圖2 (b)所示,干燥特性曲線中的臨界含水量均處于較低的水平(圖2為0.044)。這也從另一個角證明了列管回轉(zhuǎn)干燥的過熱蒸汽傳質(zhì)機(jī)理。
進(jìn)入上述降速干燥階段后,隨著相對攜濕氣體流量的加大,列管回轉(zhuǎn)干燥機(jī)烘干機(jī)內(nèi)傳質(zhì)機(jī)理將發(fā)生轉(zhuǎn)變,由過熱蒸汽干燥轉(zhuǎn)變?yōu)闊犸L(fēng)干燥。通常情況下,熱風(fēng)干燥比過熱蒸汽干具有較低的產(chǎn)品終含水量。因此,對于具有深度干燥要求的干燥系統(tǒng),引入攜濕氣體是必要的。利用這些特性,可以使干燥系統(tǒng)在較小的熱消耗下,獲得較高的干燥能力和較低的產(chǎn)品終水分。
列管回轉(zhuǎn)干燥機(jī)烘干機(jī)具有非常復(fù)雜的傳熱傳質(zhì)機(jī)理,本文所建立的實驗系統(tǒng)和研究結(jié)果雖然僅從一個側(cè)面對干燥機(jī)烘干機(jī)理進(jìn)行了探討,但可為下一步對列管回轉(zhuǎn)干燥機(jī)烘干機(jī)干燥機(jī)烘干機(jī)理的深入研究提供有益的幫助。
4、結(jié)論
● 攜濕氣體對列管回轉(zhuǎn)干燥機(jī)烘干機(jī)內(nèi)傳熱和傳質(zhì)過程具有顯著的影響作用。
●PTA在列管回轉(zhuǎn)干燥機(jī)烘干機(jī)內(nèi)的干燥特性曲線可分為預(yù)熱、恒速和降速三個階段。
● 存在一個使干燥速率出現(xiàn)峰值的最佳攜濕氣體流量,與單位時間內(nèi)脫水速度的比值約為0.16。
● 在恒速階段,列管回轉(zhuǎn)干燥機(jī)烘干機(jī)內(nèi)的傳熱傳質(zhì)遵循過熱蒸汽干燥機(jī)烘干機(jī)理。