某公司8m2豎爐于1990年投產(chǎn),日歷作業(yè)率為89. 53%,實際作業(yè)率為93. 41%,勞動生產(chǎn)率較低。成品球強度較差,轉(zhuǎn)指數(shù)81. 41%,球團礦噸耗精礦1095kg,膨潤土消耗為51. 6kg/t。由于原料消耗高,返礦大以及其他方面原因,造成成本很高,達到了401. 75元/t。為此,1997年對豎爐進行了大修改造,對許多工藝做了改進。并在1998年8月對球團原料系統(tǒng)進行了改造。
2 球團生產(chǎn)對原料的要求
一定的粒度、適宜的水分和均勻的化學性質(zhì)是生產(chǎn)優(yōu)質(zhì)球團礦的三項基本要求。一定的細度是物料成球的必要條件。為了穩(wěn)定造球過程和獲得足夠強度的生球,精礦必須有適宜的粒度和一定的粒度組成。據(jù)國外生產(chǎn)經(jīng)驗介紹,適合造球的精礦-0. 045mm(- 325目)部分應該控制在60%~80%之間,或-0. 074mm(- 200目)部分應控制在90%以上,尤其是其中- 20ym部分不得少于20%,造球?qū)V粉上限要求不超過0.2mm。可見,球團廠家對精礦粉的粒度要求都很高的,這樣就使選礦成本增高,相應使原料價格增加。
3 原料分析
從精礦使用看,由于自產(chǎn)精礦不能滿足生產(chǎn)需求.需外購部分細精礦。自產(chǎn)和外購精礦品位都較高,但粒度距工藝要求相差較遠。另外,外購精礦雜亂、品位不穩(wěn)、粒度不穩(wěn),而且長期存放后,表面活性大大降低,成球困難,這種狀況在冬季生產(chǎn)反應尤為明顯。車間使用原料見表1、表2。
表1精礦物理化指標
名稱 | TFe | SiO2 | C | S | 粒度(-200目) | 水分 |
球團精礦 | 65.01 | 5.88 | 2.44 | 0.080 | 56.6 | 8.1 |
礦山精礦 | 65.63 | 4.65 | 1.31 | 0.093 | 61.0 | 9.5 |
名稱 | SiO2 | CaO | Fe | S | 膠質(zhì)價 | 粒度(-200目) | 水分 |
赤峰 | 59.93 | 1.76 | 2.88 | 0.012 | 497 | 96.5 | 8.5 |
沙海 | 60.00 | 2.63 | 3.12 | 0.016 | 190 | 94.0 | 8.2 |
西溝 | 63.32 | 2.39 | 3.20 | 0.032 | 160 | 63.5 | 9.2 |
那家公司1997年10月球團改造后,實現(xiàn)了年產(chǎn)30萬t球團的生產(chǎn)能力,球團的質(zhì)量指標還達不到要求,成本費用較高。其主要原因就是精礦粒度距工藝要求相差較大,膨潤土配入量踞高不下,導致生球質(zhì)量差、返礦大,球團品位下降。更主要的是降低了高爐的利用系數(shù),增大了燃料消耗。為了提高球團礦的質(zhì)量,降低成本,進一步挖潛改造,提高經(jīng)濟效益。計劃在球團原料上料線上增設原料潤磨工藝設施,實現(xiàn)精礦粒度的進一步細化,提高其顆粒表面活性,滿足工藝要求。
5 技術(shù)改造總體方案
將庫存的兩臺歷21OOmm×3000mm濫流式球磨機改造成潤式球磨機。
5.1生產(chǎn)工藝流程
將潤式球磨機安裝在原料干燥工序之后,烘干后的原料通過2#膠帶機分離一半的料經(jīng)3#膠帶機送到螺旋輸送機。由螺旋輸送機送入潤式球磨機,經(jīng)過潤式球磨機后,由周邊排料口排入4#膠帶機再返回原來的2#膠帶運輸機,送入造球室。工藝布置如圖1所示。
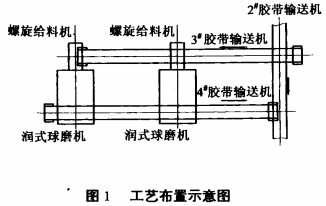
5.2投術(shù)改造的主要內(nèi)容
在原來2#膠帶運輸機上安裝分料器。將兩臺潤式球磨機安裝在材料庫所占的12m×24m的廠房內(nèi),增加兩條皮帶機通廊與上料的2#膠帶運輸機連接,實現(xiàn)分料、潤磨和造球工藝。
5.2.1潤磨機的改造
原Φ2100mm×3000mm溢流型球磨機改造成潤磨機,采取了以下措施:
1)進料:由原來的蝸形給料器給料,改為螺旋輸送機強制給料,放堵塞,葉片外緣鑲嵌硬質(zhì)合金片,提高工作壽命。
2)排料:原來是軸端捧料,改為周邊排料。在原來筒體上開孔260mm×320mm,10個,在開孔部位鑲篩板,篩板材料為錳鋼。將原來的軸端出料口改為螺旋狀的鋼球孔。
3)傳動部分移到進料端。
4)主軸承原來是油杯滴油潤滑,改為稀油集中循環(huán)潤滑。配備潤滑站。
5)筒體內(nèi)部襯板,基本上還用原來的襯板,根據(jù)具體尺寸做相應的改動。
6)取消原來的供水部分。
7)在排料口部分增加封閉的出料口罩,內(nèi)襯為薄高分子聚乙烯襯板。
8)改造后的潤式球磨機簡圖如圖2所示。
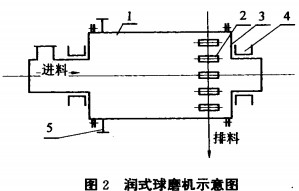
5.2.2潤磨機的主要性能參數(shù)
潤磨機尺寸:Φ2100mm×3000mm
裝球量:30t(充填率25%)
生產(chǎn)能力:30t/h
傳動型式:邊緣單傳動
磨體轉(zhuǎn)速:23. 8r/min
主電機:210kW、8級、380V
螺旋給料機:葉輪直徑Φ400mm
排料方式:周邊排料
5. 3.3潤磨機配套機械
兩條B=650mm,V=1.25m/s的膠帶輸送機,一條將從2#膠帶機介出的料供給螺旋輸送機。另一條接潤磨機排出的料,送回2#膠帶機直接送入造球室。
兩臺螺旋輸送機供潤式球磨機料,葉輪直徑Φ400mm。
6 改造效果
6.1增加潤磨機放寬了工藝對原料的要求
進廠原料范圍可適當放寬,- 200目達到50%左右的原料即可進廠,有利于豎爐球團技術(shù)的發(fā)展和礦資源開發(fā)利用,經(jīng)過潤磨機磨,粒度- 200目可達到64. 5%。
6.2可降低膨潤土消耗,提高球團礦品位
使用潤磨機后,膨潤土配比可降低至2.2%~3.0%,在原料不變的情況下,球團礦的品位可由原來的61%提高至62%—63. 5%。
6.3提高了生球產(chǎn)量和質(zhì)量
原料經(jīng)潤磨機后直接用來造球,精礦粉的溫度在造球前得到了提高,熱焓量增加,有利于成球。另一方面,細磨物料顆粒變細,單位體積明顯增加,表面活性增加,親水性能增強,有利于物料成核、母球的長大,縮短成球時間,提高了產(chǎn)量和質(zhì)量,使得造球機的利用系數(shù)提高。
6.4可適量配加入球團返礦或其他鐵料
球團返礦添加后,可使球團礦還原膨脹率減小,控制異常膨脹,從而大大有利于高爐操作穩(wěn)定順行,但返礦添加必須經(jīng)過細磨,否則0.2mm以上的返礦很難成球。
7 結(jié)論
通過對8m2豎爐球團原料潤磨進行技術(shù)改造,增加潤磨工藝后,經(jīng)過設備改造、安裝、調(diào)試,該系統(tǒng)已經(jīng)于1999年3月熱試車成功。根據(jù)設備的運行情況來看,對舊設備的改裝及原料系統(tǒng)的技術(shù)改造是合理的、成功的,提高了產(chǎn)品質(zhì)量,降低了成本。
三門峽富通新能源科技有限公司不但銷售球磨機還銷售雷蒙磨、雷蒙磨粉機、雷蒙磨配件等。